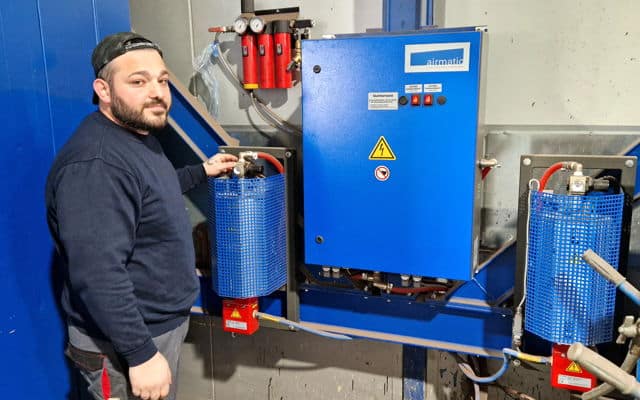
Baisch Metall is one of the largest steel component manufacturers in southern Germany. Its products are shipped all over the world via well-known customers such as Liebherr. The production area of over 7,500 square meters mainly produces crane parts, lattice structures and heavy-duty modules. The company wants to continue to expand and relies on reliable quality - including when it comes to painting surfaces.
Göksal Merkit is Head of Colour at Baisch MetallHe knows his customers' requirements very well. "The specifications often contain precise μm specifications for the individual paint layers, and a maximum total layer thickness is specified," explains the master painter, adding: "Only with the help of the airmatic system can we achieve these precise values."
The airmatic atomization optimization can be used with any air-supported application technology. It can be integrated into the existing system technology with little effort. The compressed air is fed via the airmatic system through a specially developed high-voltage unit (EMP). The neutral electrical field ensures homogeneous and charge-neutral droplets.
"We noticed the difference straight away," reports master painter Merkit, adding: "The paint was distributed evenly on the steel and there was significantly less overspray in the air." In addition, the compressed air is heated by the airmatic system - or cooled if necessary. "The heating and ionization of the compressed air ensure the same process conditions all year round," confirms Göksal Merkit. This means that the painting result is just as optimal on hot summer days as in the cold winter months.
In addition to the amount of paint, the company has also reduced the amount of compressed air by using the airmatic system. "At first it felt like driving with the handbrake on," explain the painters. "However, the more even layer thicknesses and the reduced effort required for the finishing work quickly convinced us and resulted in an increase in surface quality and also made our rework and booth cleaning easier."
The management handled the purchase of the airmatic system. "We think it is important to make our system technology as efficient and future-proof as possible in addition to renewable energy sources," explains Managing Director Michael Schirmer. With the airmatic system, the company has achieved savings in paint and energy and sustainably increased surface quality.
In this way, Baisch Metall is responding to the cost pressure on resources and energy and increasing customer demands with sensible technologies. An important step to combine economic efficiency and sustainability and to remain competitive in the future.