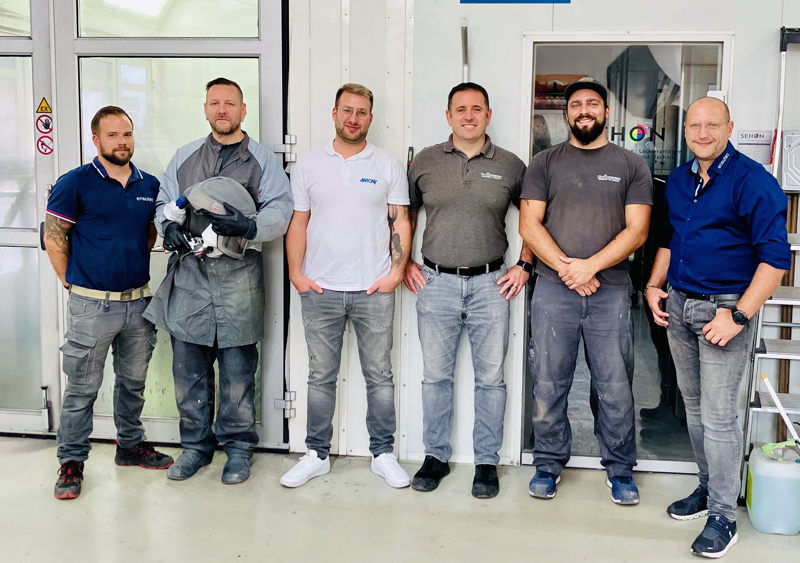
The industry magazine "schaden.news" has published an interesting article: A paint company reports how it came to optimize airmatic atomization and how the process goes from ordering to commissioning in the workshop. We are publishing the article by schaden.news editor René Förster verbatim:
airmatic atomization optimization: Faster throughput times and improved surface quality
Process times that are too long, use expensive materials and require a lot of finishing work at the end of the repair process? The company wants to show that there is potential for optimization in these areas. ensutec Products GmbH from Langenenslingen K&L companies. With its airmatic atomization technology, the workshop equipment supplier offers, among other things, year-round air conditioning of the spray air, which leads to constant processing temperatures in summer and winter. In addition, according to ensutec owner Thomas Mayer, the EMP unit ensures a homogeneous and fine spray pattern with uniform droplets, which significantly reduces overspray in the paint booth.
“On the same day we noticed the first differences in the paintwork”
In order to see how the technology works under real workshop conditions, the team from the Baden-Württemberg manufacturer, together with its trading partner Antony Autolack GmbH Interested parties have the opportunity to test an airmatic system live in their own company.
This offer was also used by the Autohaus Graf Hardenberg in Tuttlingen, after Antony sales representative Christian Joos demonstrated the possibilities for process optimization. A corresponding test system was provided by ensutec and connected to the existing painting technology in the car dealership. Afterwards, everyone involved received an introduction from ensutec project manager Viktor Otto, who put the system into operation with his colleague.
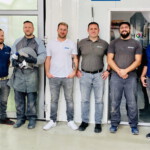
The painters remember: "We noticed the first differences in the paintwork that same day. The particularly even spray pattern led to less overspray and thus to more efficient use of paint and compressed air." In addition, the finishing work was significantly reduced due to the improved surface quality.
Manuel Schmelovski, head of the bodywork and paint department at Graf Hardenberg, adds: “We noticed that we have to do less sanding and polishing and can therefore generate faster throughput times.”
Shortly thereafter, the management decided to purchase an airmatic atomization optimization system.
airmatic atomization optimization: Easy on-site installation
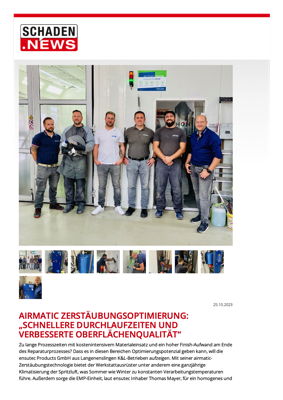
The final installation of the airmatic system in Tuttlingen was carried out in just a few steps. After the system was delivered by a shipping company, the desired installation location was determined with those responsible at Graf Hardenberg. The fitters used the option of setting up individual components separately due to the frequent space problems on site.
In the next step, the technicians connected the EMP unit and the main cabinet to the existing compressed air supply. This was followed by cabling and a comprehensive electronics check.
Finally, the ensutec team started the test run of the system, during which the desired process parameters were set. During commissioning, a detailed briefing and training session was held for all those responsible, during which any open questions were clarified.
“From the first inquiry through the test phase to the installation and final commissioning, we always felt that we were looked after professionally,” confirms department head Manuel Schmelovski.
René Förster