airmatic revolution
Reliable painting all year round
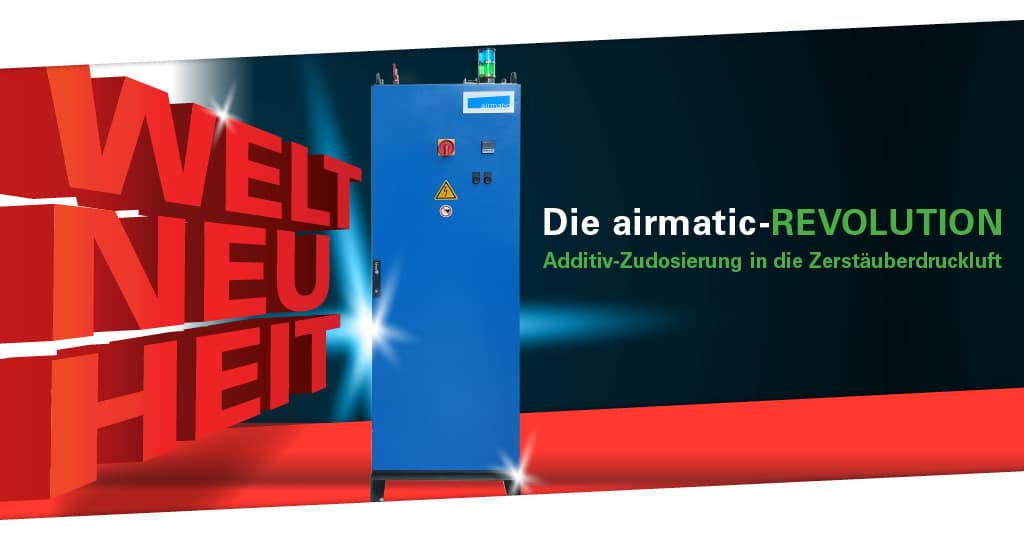
The airmatic revolution is the latest development from ensutec Products GmbH. It is used to treat atomizer compressed air: thanks to a controlled minimum air humidity, it guarantees consistent parameters and process reliability all year round.
Painting is mwith the airmatic revolution better, faster and, above all, cheaper.
And what's more, reducing energy consumption protects our environment, day in, day out! Environment protected, every day!
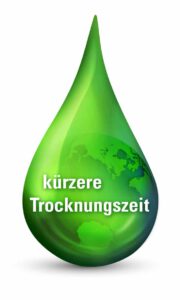
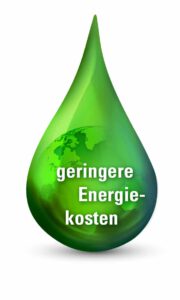
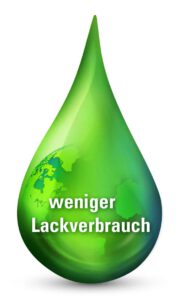
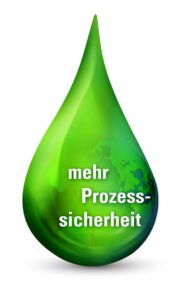
What do we do?
We enrich your atomizer air with our femaBlue 2901 base additive. This enables you to achieve an optimum reaction of your paints with the required moisture at the optimum time.
In addition to adding the base additive, it is also possible to inject other paint-specific additives directly into the spray jet via the atomizer air.
In this way, you can significantly reduce your energy costs. And you can also reduce the amount of liquid used in conventional processes to humidify the cabin supply air.
Minimal use of humidity with minimal energy costs and at the same time the highest surface quality, without the otherwise necessary humidification of the entire cabin air: what more could you want?
The effect
The atomizing air is enriched with the femaBlue 2901 base additive: this is how you achieve unique, first-class paint surfaces!
When spraying your paint, the reaction process of the paint is already activated by the additive in the paint jet. This can significantly reduce the energy required for the drying process.
Because the atomizing air is enriched directly in the paint jet, a minimum use of additive can be guaranteed by reacting a very large reactive paint surface with very many very small drops of paint.
At the same time, the reliable use of the additive ensures the same process conditions all year round - regardless of weather-related and seasonal influences!
Is that really true?
In the meantime, several well-known paint manufacturers and paint groups have tested the airmatic revolution positively. All tests have confirmed the unique effect of our airmatic revolution!
How it works
Initial situation
for modern coating systems
- Constantly changing climatic conditions
- Year-round process reliability is not guaranteed
- Many different work processes in the paint booth
- Optimum painting process depends on climatic room conditions
- Relative humidity in the paint booth often insufficient for the requirements of various paint systems
The state
of the art
Technical humidification of the cabin air is necessary to achieve 40-60% relative humidity. Ndisadvantages:
- Humidification of large volumes of air necessary
- High demand for demineralized water
- High energy costs
- Risk of contamination
- Long process times due to changing climatic conditions in the painting/drying booth
- Rusting paint booths
The technical future: our airmatic revolution
The airmatic revolution consists of a reactor with Nanotechnology: Here, the base additive is mixed into the atomizer air. As an option, other specially selected additives can be mixed in.
At the same time, the atomizer air, which is heated in a special ratio, prevents condensation of the compressed air enriched with a high relative humidity. This ensures the highest painting quality: better film formation, better flow, higher application efficiency.
Static charging of the surfaces is avoided!
The painter is happy about the “revolution”
- High paint quality
- Better course
- Better paint level
- Less runner formation
- Less dust and dirt inclusions
- Reduction in finishing costs
- Less overspray
- Pleasant painting conditions
- Reliable maintenance of the required humidity under changing climatic conditions
- The reaction with the paint and thus the hardening already takes place in the paint jet
- The painter does not have to change the way he works when using the airmatic revolution
The innovative paint hose
- With integrated heating system
- With PID control
- With ATEX approval
- Extremely light and flexible
- Breathing air use possible
- Different lengths available
The advantages for the paint store
- Can also be retrofitted in existing systems without great effort
- Very fast amortization
- Elimination of cabin air humidification
- Paint savings of 10 to 20%
- Fastest drying and curing time
- Capacity increase
- High quality
- Reduced to no oven drying necessary
- Material and energy efficiency
- Process reliability
- Reactor with nanotechnology allows the addition of other specially selectable additives