airmatic atomization optimization in field trial
The effect on your application!
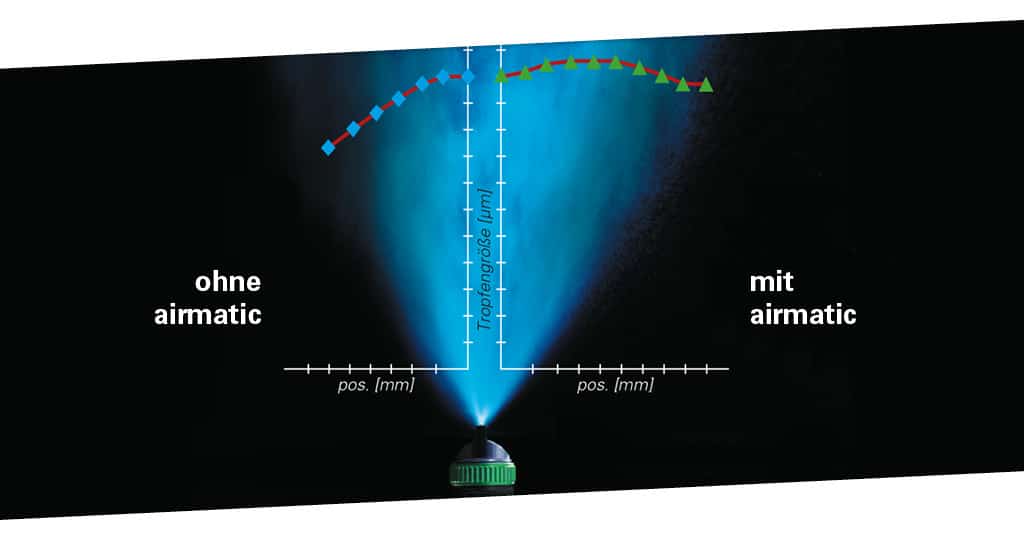
The aim of the DBU project
As part of pilot plant and field tests, we are investigating the extent to which the use of airmatic Economic and ecological improvements in paint application can be achieved. In addition, it should be considered to what extent further system optimizations can be carried out. The Esslingen University of Applied Sciences is responsible for the scientific monitoring and evaluation of the investigations and supports possible further developments and extensions.
results of a field trial
As part of a field test, the influence of airmatic on the practical Application of a clear coat to plastic and metal substrates. The following parameters and target variables were determined:
primary atomizer properties:
• Change in the distribution of the mean droplet size (Volume median Dv(50))
• Change in Sb50 (spray jet width at half maximum layer thickness)
• Transfer efficiency (AWG)
Properties of the applied paint film:
• Change in the average layer thickness
• Appearance
Air atomizers were used, with the air volumes used in the following ranges:
Horn air: 88 – 106 Nl/min
Atomizer air: 109 – 135 Nl/min
The color quantities of the clear coat used were kept constant.
The results
1. Distribution of the mean droplet size Dv(50)
The measurement was carried out using laser diffraction spectrometry.
It is clear that when using the airmatic atomization optimization, the radial distributions of the mean droplet sizes are significantly homogenized.
An increasing refinement of the spray towards the edge no longer takes place.
2. Appearance/Structure
Measurements using WaveScan showed that the changes shown in the Spray jet properties do not affect the appearance.
Long and short wave values as well as the DoI comply with the specifications without restrictions.
3. Layer thickness width at half layer thickness maximum (Sb50)
Due to the change in atomization, also to a change in the layer thickness distribution, ie the characteristic beam widths Sb50 of the obtained Dynamic spray patterns are increased by the airmatic atomization optimization. The spray patterns were measured using 3 lanes per substrate (total 333 measuring points) automatically on a coating thickness measuring table. the high number of individual measurements and a double Implementation minimized measurement errors and Results are statistically secured.
With the help of parallel volume flow measurements, It can be ruled out that the changes in the atomization and dynamic spray patterns from changed air volumes result.
When using airmatic, the air volumes remained in the scope of measurement accuracy (approx. ± 2%) constant.
5. Average layer thicknesses
In accordance with the improvements received The application efficiency also increased the average layer thickness in a range between 1 and 3 μm can be observed, ie at medium Layer thicknesses of approx. 20 μm between 5 and 15 μm.
With the same target layer thickness, the use of the airmatic reduces the amount of paint used by be reduced by the same percentage.
The conclusion
The following findings were obtained during the field trial:
By using airmatic atomization optimization
• the paint spray becomes significantly more uniform in terms of the average diameter,
• the dynamic spray patterns widen by approx. 15 – 25 %,
• the application efficiency for plastic substrates increases by 5 – 6.5%,
• the average layer thicknesses increase by 10% for plastic substrates and by 7% for metal substrates,
• There is no noticeable change in the appearance or paint structure.
• These results were obtained independently of the application parameters set.
• The installation of the airmatic does not cause any change in any preset air volume flows when regulating pressure.
• The mean layer thicknesses were tested positive for statistical significance.
In total, the use of airmatic atomization optimization results in a broadening of the dynamic spray pattern and at the same time a significant increase in the application efficiency.
This results in potential paint savings of 5 to 15 percent!