airmatic and powder coating
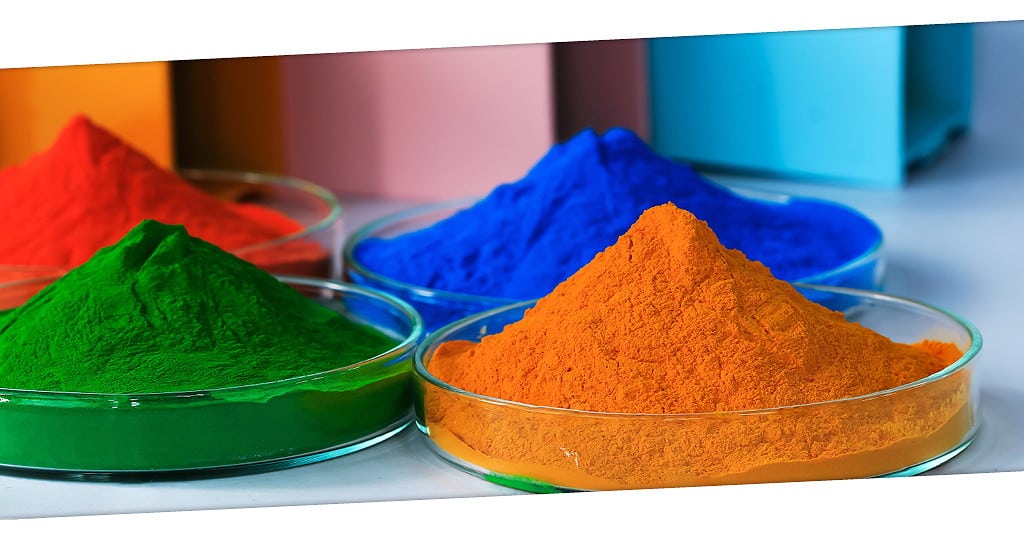
The state of the art
In classic powder coating or powder painting, the surfaces of electrically conductive workpieces are coated with powder paint. The corresponding technology was developed primarily in the USA, but the guns for electrostatic powder coating were also launched in Europe from the very beginning. More or less at the same time - between 1966 and 1973.
There are various methods for charging the paint particles, which depend on the technical equipment of the spray gun used.
The Corona application
When charging by ionization, the paint particles are guided along an electrode that has a voltage of up to 100 kV. The high voltage ionizes the air surrounding the particles.
When the paint particles pass through the electric field between the grounded workpiece and the high-voltage electrode of the spray gun, air ions accumulate on their surface. However, these only account for 1 to 3 percent of the air ions present; the remaining free ions are referred to as space charge.
As part of the so-called low-ion corona charging, these ions are absorbed by an additional electrode at the tip of the powder spray gun, so that their charge is dissipated.
Due to a suboptimal removal of the disruptive free ions, an accumulation of electrostatic charges in the form of Faraday cages occurs on the workpiece.
These electric fields cause disruptive properties when painting conductive workpieces, resulting in insufficient penetration depth and edge build-up (so-called picture frame effect), which have adverse effects on the paintwork and its quality.
Our state of development technology
With airmatic technology, you can reduce these disruptive electrostatic fields and ensure optimized application of powder coatings.
The airmatic technology uses EMP technology to improve the penetration depth of the powder into corners and edges. Geometrically difficult components can be coated reliably and with high quality.
The airmatic functional earthing simultaneously improves the electrostatic effect by reducing the field lines on corners and inner edges, thus reducing the formation of Faraday cages. The result is a more even distribution of layer thickness, which reduces picture frame effects.
The airmatic functional earthing is an additional installation component and does not perform a protective earthing function.
Together, airmatic atomization optimization and airmatic functional grounding form an effective duo that increases the application efficiency, especially of the fine grain portion, while simultaneously improving coverage and penetration depth.
Targeted – Quality-enhancing!
As functional additional components of a modern powder coating, our systems ensure optimization of the regular operation of the electrostatic powder coating application and achieve high quality surfaces!
Application method
- Electrostatic powder coating
- Corona powder gun technology
System technology
- hand application
- fully automatic flow systems with lifting frame
- robot application
Advantages
- Powder coating savings of up to 15 %
- Compressed air savings of up to 30 %
- More homogeneous layer thickness distribution
- Reduction of Faraday cages
- Reduced edge build-up and therefore fewer picture frame effects
- Better penetration depth in corners and edges
Our references
Here you can see a small selection of companies that rely on our proven airmatic technology in the field of powder coating. If you have any questions about the individual references, please feel free to contact us!